Swabbing is an excellent way for businesses to increase the useful lifespan of a well while also reducing their own costs and any associated impact on the environment. Swabbing is used in conjunction with methods such as hydraulic fracturing (“fracking“), in order to recover more from the well. Understanding this process is vital to improving the cost-effectiveness of every well drilled.
The Process of Swabbing a Well
When fracking fluids are generally introduced into the well. These fluids can then be recovered via swabbing. Swabbing will remove the fluids that are currently within the well, which alters the pressure differential in the well; this often leads to more oil and gas being able to be recovered. The fluids that are used through the process of fracking may be mixed with natural gas and oil, and the pressure involved may be holding back recoverable resources.
Well production will generally fall off over time, but processes such as swabbing can be used to recover resources after the well is considered to be depleted. In so doing, this reduces the amount of time that the company needs to use drilling new wells and exploring new wells. Many older wells can be successfully swabbed before they are considered to be completely depleted or abandoned. Once the well is swabbed, production levels may be restored for some time.
The Challenges Involved in Swabbing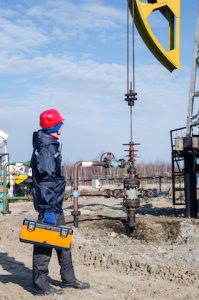
Swabbing isn’t just a technical process. Not only does the equipment need to be right, but it also needs to be handled correctly. Operators, over time, develop a feel for swabbing; for running the machine alongside the well pressures and for getting the best yields. This is a very intuitive process, because it relies on sounds from the well and the depth at which the well is being swabbed. A good operator will have far better yields involved in swabbing than an inexperienced operator. Naturally the machinery and equipment also matters.
The swabbing process is completed by machines with both a winch and a cable. The better the machine, the more service it will be able to see before it requires maintenance and repairs… and therefore the more cost-effective it will be. There are a variety of sizes of web machines, depending on the size and the depth of the well that needs to be swabbed.
The Process of Swabbing a Well
A swabbing rig is backed close to the well and the operator raises the mast. The mast has to be aligned with the center of the well. The cable and tools are lowered, which includes a weight bar, jars, and swab cup tools. Swap cups seal the inside of the well so that the swabbing can be completed. Once the tools reach the fluid level, the fluids are moved up and lifted out of the well. Usually this will continue until approximately six barrels of fluid have been raised from the well. Some wells may need more. The pressure will be relieved and the well will begin to flow again.
Much of the equipment that is used throughout the process of swabbing still uses designs that were first developed in the 1800s. But Tiger General LLC uses advanced designs including dirt to winch drum hydraulic drives. These drives are far more efficient than traditional old-fashioned mechanical chain drives, which are also more difficult to keep in service.
Tiger General’s swab master machines will require far less maintenance and be more cost-effective than traditional swab rigs, allowing companies to keep their wells in service at a far more efficient and cheaper price. Most of Tiger General LLC’s equipment can get a 15 year design life before requiring an overhaul, and the overhaul is built to be simple and fast. Comparatively, other rigs will need to be overhauled within five to eight years. For more information about Tiger General’s swab master rigs, you can take a look at the current inventory.